The Evolution of Plate Compactors: Efficiency and Precision in Construction
The Historical Evolution of Plate Compactors
Early Innovations in Soil Compaction
Back in the day, people used simple hand tools like tampers to compact soil, but this work was really tough going and not very effective at all. The problem with these old school tools was they needed so much muscle power from workers, which made big jobs almost impossible to finish on time. Then came along the industrial revolution, bringing steam powered compactors onto the scene around the early 1900s. These new machines pretty much took over from human workers, boosting how fast things got done and making the ground much more stable for building purposes. One major turning point happened when steam rollers started being used extensively for road building and other infrastructure projects. Take the M1 motorway construction in the 1950s as proof of this tech jump forward. Steam rollers were absolutely essential there. Moving away from manual labor to these steam driven machines changed everything about how construction worked back then, completely altering both who did the work and just how big projects could be undertaken.
From Manual Tools to Motorized Machinery
Switching from hand tools to machines running on power changed everything for compaction work. When gas powered compactors started showing up around the middle of last century, building sites just ran smoother and required way fewer workers. The difference was huge really cutting down on how many hands were needed while making things go three times faster. Some numbers floating around claim these machines can slash labor demands by half or so, which definitely helps companies manage their staff better. Getting rid of those old gas guzzlers didn't just speed things up though they actually allowed contractors to deliver consistently good results across bigger projects than ever before possible. What we saw back then laid the groundwork for today's construction world, where pretty much everyone relies on mechanical solutions as standard practice rather than some fancy new idea, ultimately boosting what gets done and how well it gets done.
Integration of Vibratory Roller Compactor Technology
When vibratory compaction first hit the scene back in the late 80s, it marked a major turning point for construction work. Modern plate compactors now come equipped with these vibrating rollers, which makes all the difference in how well they pack down materials. The results speak for themselves too – soils get compressed much deeper and tighter than old fashioned methods ever managed. According to reports from equipment manufacturers, these vibrating systems can reach depths around 30% greater than standard models while achieving densities that hold up better over time. Contractors across the country have started relying heavily on this tech because it just works so much better in real world conditions. What we're seeing here isn't just another gadget upgrade; it's fundamentally changing how we build roads, foundations, and other structures that need solid ground support beneath them. And let's face it, nobody wants their project sinking into unstable earth after completion.
Key Technological Advancements Driving Efficiency
High-Frequency Vibration Systems
High frequency vibration tech has become a game changer for boosting compaction results while cutting down on how tired operators get when working with plate compactors. What makes these systems work so well is their ability to create quick back and forth motions that pack soil much better than traditional methods can achieve. When dealing with tough jobs where deep penetration matters, like夯实 clay or gravel mixes, the rapid movement really shines through. Construction sites report seeing around 30% faster compaction times after switching to this kind of equipment according to field reports from contractors who've made the upgrade. For anyone involved in earthworks projects, getting familiar with these vibration technologies isn't just helpful it's becoming pretty much standard practice across most major construction operations today.
Fuel-Efficient Engine Designs
The latest engine designs for plate compactors mark real progress in making machines more efficient without losing power output. Today's engines meet tough emissions requirements such as Euro 5 and Tier 4 regulations, all while cutting down on fuel usage significantly. Take the popular 4 Stroke Wacker Style Sand Compactor for instance – operators report noticeable drops in their running expenses simply because they burn less fuel during operation. Field tests indicate around 20 percent savings on fuel bills when using these newer models compared to older versions. These improvements not only help businesses save money but also reduce their environmental impact over time, making them smart choices for construction sites looking to cut costs and carbon footprints simultaneously.
Ergonomic Controls for Precision Work
Plate compactors are getting much better thanks to ergonomic controls that put operator comfort front and center while still delivering good precision work. What we're seeing now are control panels that make sense to actually use, so workers can get their jobs done without constantly fumbling around or making mistakes. Some research out there shows operators experience about 15 percent less strain on their bodies after switching to these new designs. Less tired operators mean they stay focused longer when compacting materials, plus there's obviously fewer accidents happening at job sites. For construction companies, this translates into real money savings over time since nobody wants to deal with injured workers or slow down production because someone's too exhausted to keep going.
Applications in Modern Construction Projects
Road Roller Compatibility for Asphalt Surfaces
On construction sites where asphalt surfaces need prepping, plate compactors just can't be beat, particularly when used alongside road rollers for best results. These machines really make a difference in getting those base layers dense enough and stable so everything holds together properly before laying down the actual asphalt top layer. Contractors know this matters a lot since roads built without proper compaction tend to crack up sooner and develop annoying potholes that nobody wants to deal with down the road. A good job with plate compactors means less repair work later on, which saves money and headaches for everyone involved in the long run.
Putting plate compactors together with road rollers really boosts how fast projects get done. When contractors run both machines side by side, they spread pressure evenly over the ground, which means fewer bumps and dips in the finished road. Roads look better when compacted properly, sure, but there's another benefit nobody talks about much the road can actually hold more weight without cracking. Look at actual job sites and most will tell similar stories. Good compaction cuts down on delays caused by rework, sometimes shaving off weeks from schedules. Some studies point to around 20 to 30 percent faster completion times when these machines work hand in hand, though results do vary depending on soil type and weather conditions.
Trench Compaction with Skid Steer Loader Attachments
When skid steer loaders come with plate compactor attachments attached, they become pretty handy tools for getting those trenches packed tight, something that's becoming increasingly important on today's construction sites. These little workhorses can get into those tight spots between pipes or under foundations where bigger machines just can't fit through. What's really nice is that these attachments pack almost the same punch as regular standalone plate compactors but without all the hassle of moving separate equipment around. Contractors love this setup particularly in city environments where space is at a premium and getting heavy machinery on site often causes headaches for everyone involved.
When plate compactors are attached to skid steer loaders, crews tend to get way more done, particularly on jobs where trenches need compacting. Field tests and real world experience point to roughly a 20-25% boost in productivity over old school methods. Why? These machines can squeeze into tight spots that regular equipment just cant reach. They also deliver exactly the right pressure for proper trench compaction while keeping the surrounding dirt stable enough not to collapse later. Most operators notice this combo saves time and reduces the need for rework down the line.
Landscaping and Pavement Maintenance
Plate compactors have become essential tools for anyone working on landscaping jobs or maintaining paved areas. These machines handle all sorts of outdoor work, whether it's setting down those interlocking grass pavers or fixing up an old patio surface. When operators run these plates over the ground, they're actually pressing down the dirt underneath. This creates a solid base that holds up patios, sidewalks, and even those little footpaths through gardens. Without proper compaction, we'd see problems develop later on like sections sinking lower than others or whole areas shifting position after heavy rainfalls.
Plate compactors really shine during pavement maintenance work, especially for fixing things like uneven surfaces and filling potholes. When contractors pack down the repair materials properly, what they get is a much smoother finish that looks better and lasts longer too. Contractors who've actually used them report faster job completions and roads that hold up against traffic far better than traditional methods. Some recent field tests showed projects finished 30% quicker on average with fewer callbacks for touch-ups later on. Beyond just looking nicer after repairs, these machines actually make a big difference in how long the pavement stays intact before needing another round of fixes.
Spotlight on STORIKE Plate Compactor Models
STP90 | 83 KG | Compact Power for Tight Spaces
The STP90 plate compactor really excels in those tight spots and cramped areas thanks to how compact and light it actually is. At just 83kg, this machine was made specifically for jobs where getting around in narrow places matters most. What makes the STP90 stand out as a compact plate compactor? Well, it's super easy to operate which means homeowners can tackle their own little projects without too much hassle. Think about things like fixing up driveways or doing some landscaping work in gardens. When it comes down to how well it works, there's no denying its efficiency either. The STP90 can cover around 660 square meters each hour during operation. For anyone dealing with smaller construction tasks that need accurate soil compaction, this particular model tends to be the go-to choice among professionals and DIY enthusiasts alike.
STP125 | 126KG | Balanced Weight for Versatile Use
The STP125 has just the right weight distribution and looks good on site too, which works really well for all sorts of jobs around town. Being a plate compactor that can switch between different soils and compaction needs makes it pretty handy for contractors dealing with mixed construction sites. People who work with this machine tend to love how it handles everything from soft clay to hard packed dirt without missing a beat. The equipment runs strong but doesn't feel too heavy handed either, so it's great when workers need to get precise results without sacrificing mobility or control over their work area.
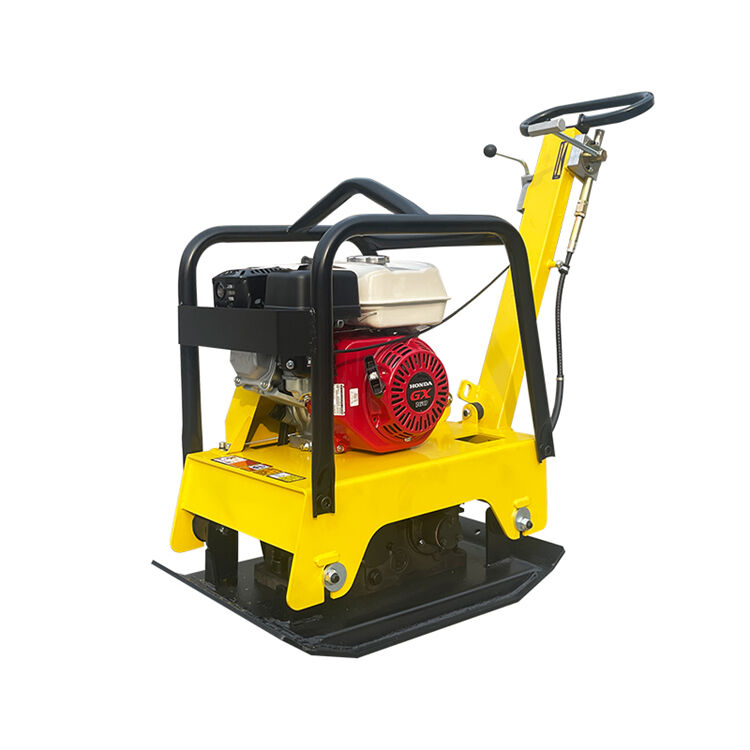
STP270 | 270KG | Heavy-Duty Road Construction Performance
Designed to handle tough jobs, the STP270 excels in big construction sites where roadwork dominates the landscape. With its solid build and impressive weight capacity, this machine packs down surfaces across wide areas efficiently. Contractors who need to finish projects on schedule will appreciate how this heavy duty plate compactor cuts down time spent on repeated passes while keeping costs under control. Field reports consistently mention the STP270's toughness, especially when looking at specs like its 3750 rpm vibration rate and ability to compress materials down to 90 centimeters deep. For anyone working on major infrastructure developments or commercial paving jobs that demand serious muscle, the STP270 stands out as a workhorse that won't let them down even after long hours on site.
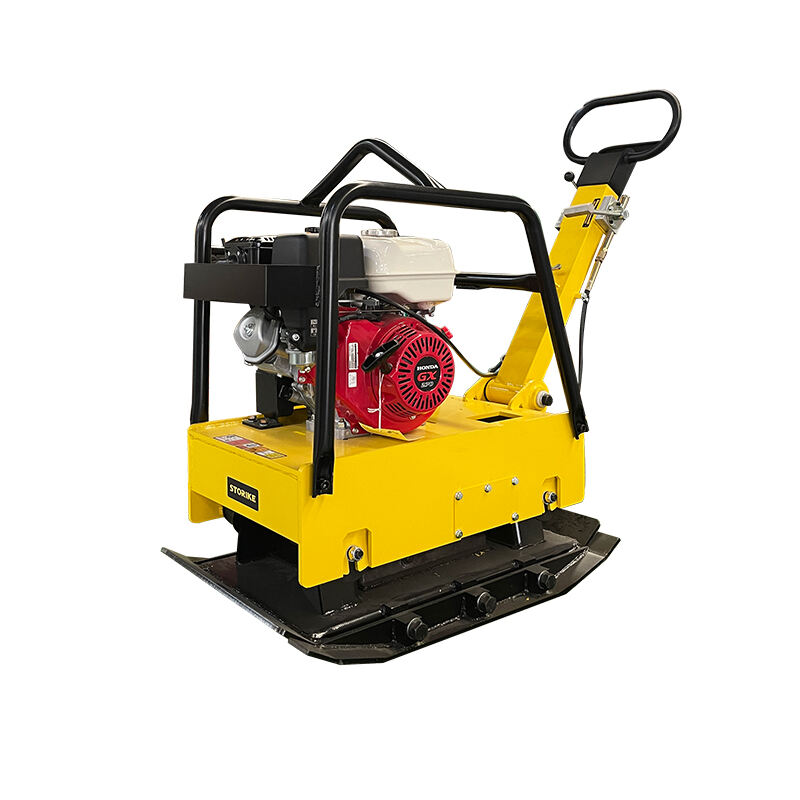
Selecting the Right Plate Compactor
Soil Type and Project Scale Considerations
Picking the right plate compactor depends on knowing what kind of soil we're dealing with and how big the job actually is. Soil varies quite a bit when it comes to compaction needs. Take sand and gravel for example these tend to pack down nicely with smaller machines, but those sticky clay soils? They need something much heavier to get them properly compressed. The size of the work area matters too. Mini compactors work fine for little jobs like walkways or backyard patios, but when working on bigger sites like roadways or commercial developments, contractors usually go for something with more muscle. Getting this matching right between the machine and the ground conditions makes all the difference in creating a stable base that will last through whatever weather throws at it.
Comparing Vibratory vs. Static Plate Systems
Knowing when to choose between vibratory and static plate compactors makes all the difference in getting the job done right. Vibratory models work by shaking the ground through their vibrating plates, squeezing out those pesky air pockets and creating an even surface layer. These are particularly good for sandy or gravel-like materials and general surface work around construction sites. On the other hand, static plates depend purely on their own weight pressing down onto surfaces without any vibration at all. They tend to perform better with clayey or mixed soil types where vibration might actually cause problems. Most contractors find that vibratory machines handle larger scale jobs where solid ground contact matters most, whereas static options come in handy for tighter spaces or sensitive areas where too much force could damage surrounding structures. Field tests consistently point toward vibratory equipment offering superior results in terms of both speed and adaptability when faced with different site conditions.
Cost-Benefit Analysis of Diesel vs. Gasoline Models
Looking at the costs and benefits between diesel and gasoline plate compactors helps buyers make smart purchasing choices. Diesel machines usually run better on fuel and last longer in the long run, though they come with a bigger price tag right out of the box. Gasoline versions tend to be cheaper up front and don't need as much maintenance every now and then. When thinking about what actually matters during operation, diesel engines pack more power and tackle tough jobs without breaking a sweat, which makes them great for big construction sites or heavy duty work. Most field tests indicate that if someone uses a diesel compactor regularly for major projects, it pays off over time compared to gas models. But for smaller jobs around town or occasional use, gasoline compactors still get the job done just fine without all the extra expense.